Find free and low-cost software
Small business owners don't always have the time or resources to find cost effective solutions that meet their needs. With cloud computing, you can pay a few dollars each month to access web-based software. These webpages will help you get started with your search.
Latest articles
15 results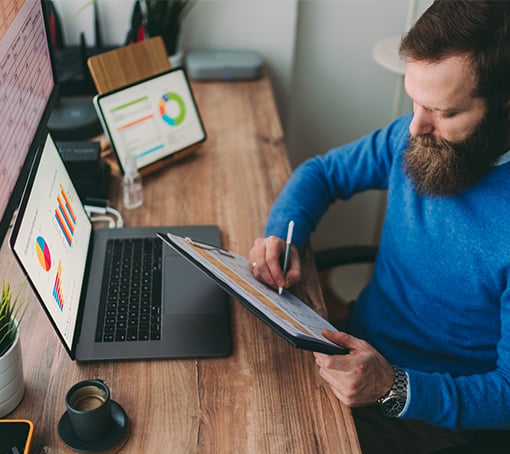
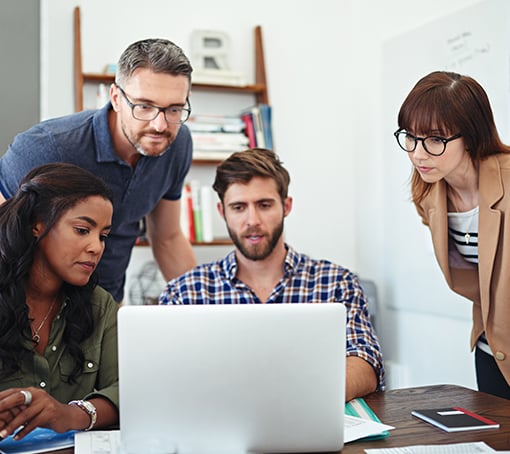
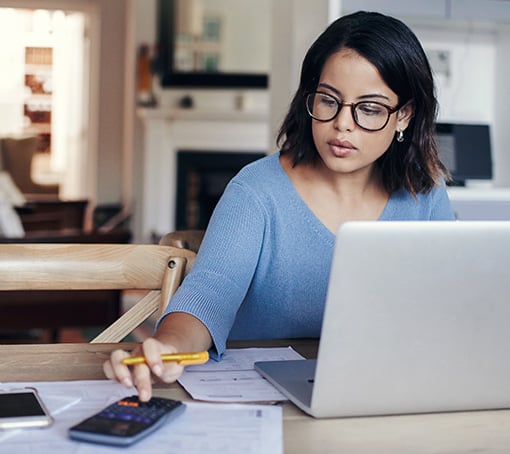
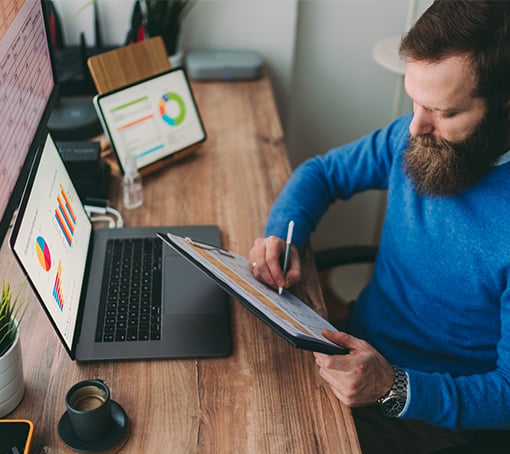
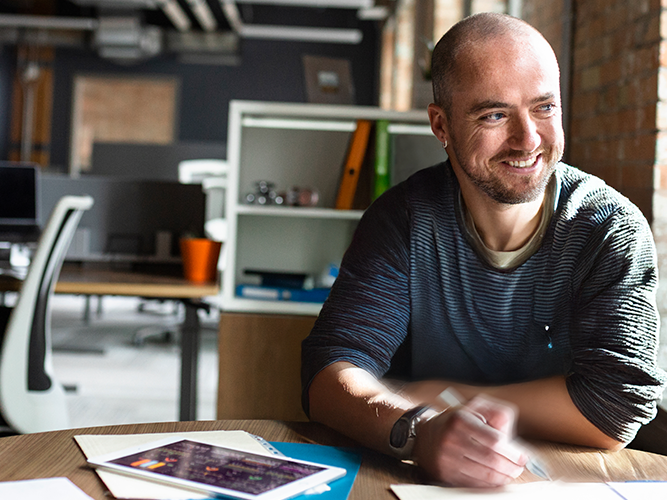
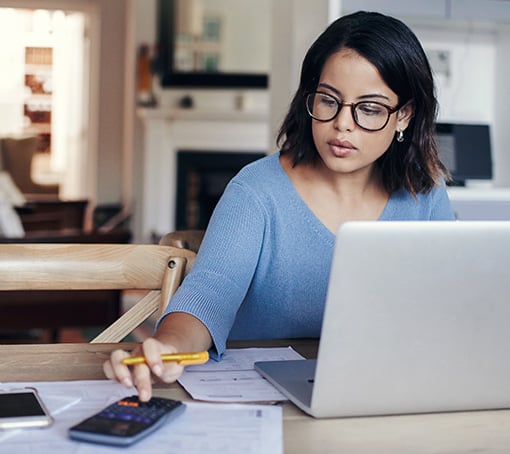
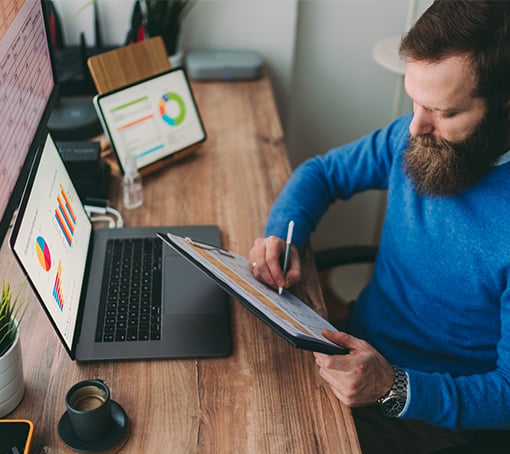
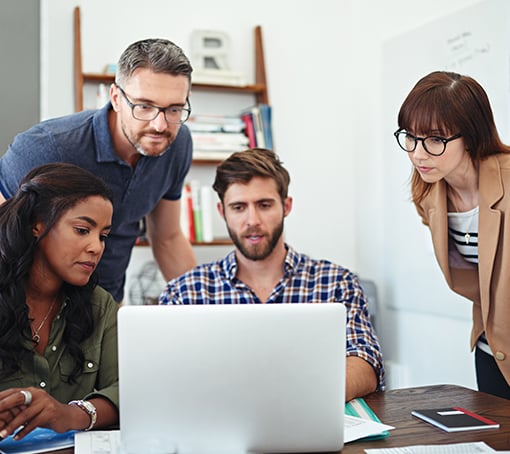
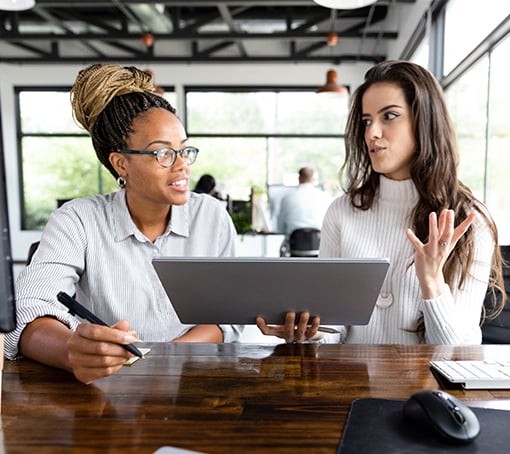
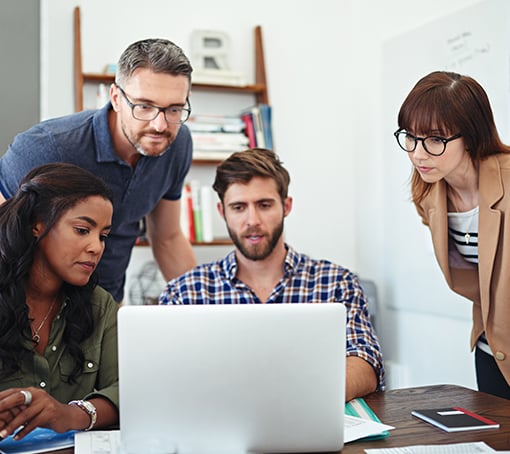
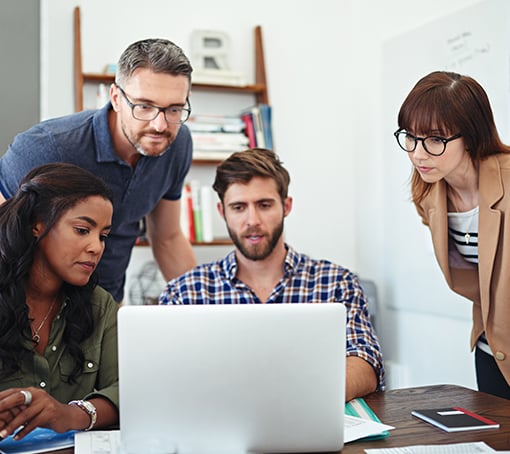
Entrepreneur's toolkit
Free tools to help you run a more successful business.
How to use technology to make your business more profitable.
Tips for avoiding common pitfalls when buying an ERP system.
Create a technology roadmap to set your priorities and plan your technology implementation.
Compare your use of digital tools to industry peers.
Use this free tool to easily benchmark your revenue and profit per employee against your industry peers.