How to minimize the environmental impact of your equipment
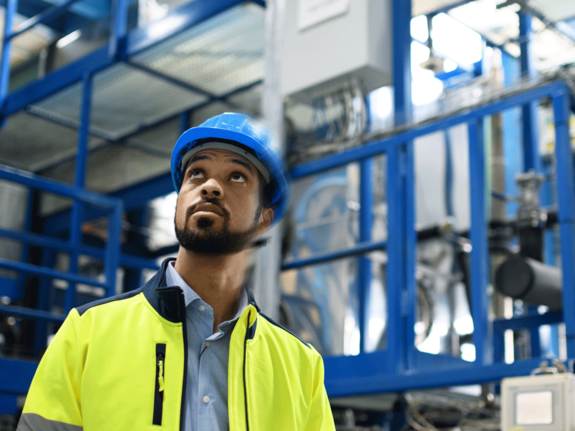
While heating, ventilation and air conditioning (HVAC) systems usually account for the majority of energy use—and greenhouse gas (GHG) emissions—there’s plenty of other equipment that also uses energy and produces emissions.
Depending on your industry, you might be running ovens, refrigerators, lift trucks, welding torches or other specialized equipment. And every building has lighting, computers and appliances that consume energy. Improving equipment performance could reduce your GHG emissions, prolong equipment life and reduce your operating costs.
Start with an energy audit
You can’t reduce what you don’t understand, so your first step should be an energy audit to gain insights into which systems and equipment use the most energy and where the biggest opportunities for reductions lie.
You don’t want to end up spending your whole efficiency budget on something that only makes up 1% of your operational energy consumption.
Kris Chapman
Consultant at Dunsky Energy + Climate Advisors
How to prepare for an energy audit
Taking these steps before your energy audit will avoid wasted time and additional costs.
- Collect documentation—This can include technical design plans; user manuals; and any other documentation related to your building, equipment and processes. You should also gather at least two years of bills for all energy sources you use. “Essentially, the more data you can provide, the better,” Chapman says.
- Make a list of equipment—A complete inventory of all equipment, as well as where it’s located and how to access it, will make it easier for your auditor to provide a thorough assessment.
- Gather input from equipment operators—To help your auditor, gather feedback from employees on equipment problems, including machines that are difficult to maintain, need repair or have any other issues.
- Have an internal expert on hand—A member of your operations team should be available to accompany the auditor. They can provide insights into equipment features, quirks and day-to-day operations.
- Set goals—Consider what you want to accomplish after your audit. Are you looking to reduce energy use and emissions by a specific amount? What’s your budget and what length of payback period are you looking for? Whatever your aims, let your auditor know so they can make recommendations with your goals in mind.
Various types of energy audits are available. Many consultants use the ASHRAE energy audit guidance, which offers three levels, ranging from a basic walk-through assessment of your equipment to an in-depth, systems-level analysis of your entire building. You can also have an audit that focuses just on specialized equipment.
At the end of the process, your auditor will deliver a report that includes recommendations for improvements. These could include process or operational changes, settings adjustments or equipment replacement. Audit reports will often note incentive programs to help cover the capital costs of improvements.
“You don’t want to end up spending your whole efficiency budget on something that only makes up 1% of your operational energy consumption,” says Kris Chapman, an consultant at Dunsky Energy + Climate Advisors.
Optimize existing equipment
After your audit, you can start to make improvements based on the recommendations. In most cases, you’ll want to start with less expensive actions that don’t involve replacing equipment.
“Unless your equipment is right at the end of its lifespan, doing what you can to ensure peak performance is usually your best first step,” says Pascal Véronneau, an energy efficiency engineer at Énergénia in Montreal.
If anything is damaged or malfunctioning, make the necessary repairs. Then ensure equipment is calibrated correctly, whether that’s the fuel–oxygen mix for combustion-based systems or sensitivity thresholds for motion sensors, presence detectors and other sensors.
Next, check your settings. Beyond the obvious, like making sure your temperature settings aren’t causing you to heat and cool the same space at the same time, look for other energy-saving adjustments.
For example, if you need to run your HVAC system constantly because one tenant operates 24 hours a day, can you set the system to close the ducts to unoccupied spaces?
Turn equipment off
Users play an important role in minimizing energy consumption. If you haven’t already done so, introduce a policy or some guidelines that call on employees to turn off equipment and lights when not in use.
Véronneau also suggests looking at how different pieces of equipment interact.
“If equipment X needs to be up and running before you can use equipment Y, train your teams not to turn on Y until X is fully warmed up,” he says. “That way you don’t have machines wasting power while they wait for others to start up.”
You can also automate many of these actions. Use motion sensors to control your lights, program machinery to come on in a certain order with the flip of a single switch, and link ventilation to presence detectors or CO2 sensors so airflow is adjusted based on real needs.
Take advantage of waste heat
Véronneau and Chapman both recommend adding waste heat recovery systems wherever possible.
“You want to get as much value as you can from the energy you use,” Chapman says. “Heat recovery systems involve some investment, but they’re usually very cost-effective, with payback within a few years.”
You can use exhaust air from your building to heat fresh air coming in. There are often also opportunities for heat recovery from industrial processes.
“Any time you can reuse heat, it’s effectively free energy because it adds nothing to your costs or your emissions,” Véronneau says. He offers the example of grocery stores, which often use waste heat from refrigerators to heat ambient air. “Any time you can intercept energy to use it for something else, you’re going to save.”
Consider fuel switching
Once you’ve made your existing equipment as efficient as possible, look into whether it makes sense to replace equipment with units that are more efficient and produce fewer carbon emissions. While this often means moving from fossil fuel-powered equipment to electric, the actual carbon impact will really depend on the fuel used to produce electricity in your area.
For example, in a province like Quebec, which generates nearly all its electricity from renewables, each kilowatt-hour (kWh) of energy generates just 2 grams of CO2-equivalent emissions. That means switching to electric equipment can dramatically reduce emissions.
On the other hand, if your business is in a province with a grid based mainly on burning coal or other fossil fuels, electric may not be your lowest-carbon option. Alberta’s grid, for example, generates 640 grams of emissions for each kWh of energy.
“In that case, sticking with existing natural gas equipment might actually be a cleaner option than going fully electric,” Véronneau says. However, he notes that electricity grids are getting cleaner all the time and that some types of electric equipment can be significantly more efficient than alternatives, so it’s worth revisiting periodically and looking carefully at all variables.
Chapman notes that incentive programs can often cover a substantial portion of the purchase cost of new, energy-efficient equipment. “There’s also the added benefit that electric equipment usually costs less to maintain, so the business case is often stronger than you might expect.”
If full replacement isn’t an option, you can still make a difference by adding equipment. For example, if you add a heat pump to a gas furnace, the system can use the heat pump during milder weather and switch to the furnace only when it’s very cold.
Measure your equipment performance regularly
A full audit every few years will keep you from going off track and alert you to new, more energy-efficient options since your last audit.
But Chapman and Véronneau say you shouldn’t depend just on audits for insights into how your equipment is performing. Instead, monitor your equipment performance on a regular basis so you can address problems as they arise.
“The simplest way is to look at your monthly energy bills,” Véronneau says. “They give you a direct comparison month-to-month and year-over-year.”
For more insights, consider installing sub-meters—smaller energy meters that can track the energy use (electricity, natural gas, fuel, etc.) of a specific zone in your building or individual piece of equipment.
These can feed into a dashboard, enabling you to monitor your energy use in real time. Some systems also offer analytics that show the amount of energy and emissions associated with each production unit and how weather affects your energy performance.
This data can be used to develop key performance indicators that help you make decisions and be tied to performance management to keep energy savings and emissions reductions a priority. You can take your efforts further by implementing the ISO 50001: Energy management standard. It allows you to incorporate best practices into your business with a framework and practical advice for developing energy management policies, setting targets, measuring results and continuously improving.
Maintain your equipment
No matter what kind of equipment you have, it requires regular maintenance to perform at its best. “And that maintenance has to go beyond: ‘Is it working?’” Véronneau says.
Energy efficiency training for maintenance teams can ensure they understand the measures you’ve put in place and prioritize energy savings in their regular checks.
Other employees who use equipment can also contribute. Provide training to ensure they know how things should work and can identify issues right away.
“Treat it like health and safety,” Véronneau says. “You need policies and support from the top, but everyone should be empowered to speak up if they notice something’s not right.”