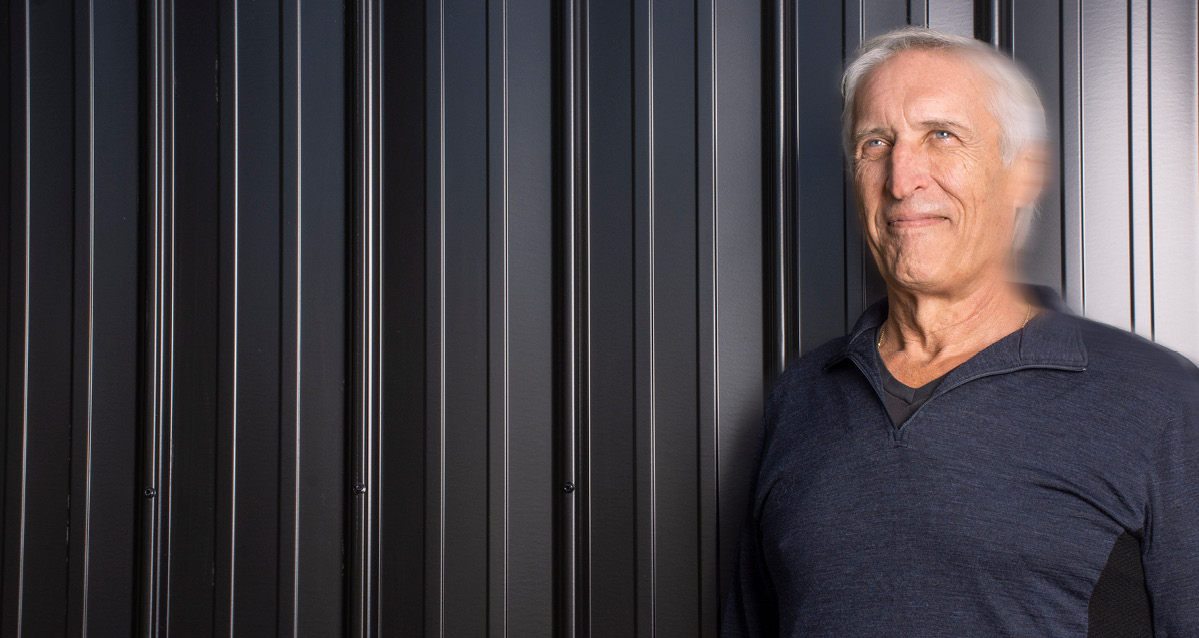
“More than once, our obsession for cutting costs turned out to be good for the environment.”
Anchor is an innovative precast concrete company that’s laser-focused on cutting costs and lowering its environmental footprint
Jeff Bradfield, CEO and owner: I own Anchor, which is a second-generation family-owned precast concrete manufacturing company in Kingston, Ontario. Operating in the concrete industry—one of the largest and most carbon-intensive industries on Earth—we believe that it is our role and responsibility to manufacture the most sustainable products possible, with the lowest carbon footprint possible. Our company’s mission is to eliminate waste in infrastructure.
Challenge
We want to make concrete structures that have the minimal impact on the environment
My wife and I raised three children. We also bought and renovated four houses. It became obvious that there is a lot of waste produced in those renovations and a lot of waste produced in the original builds.
We asked ourselves: what do we have to do to make these structures last for the next 100-plus years, with minimum materials and toxins, while maximizing their lifespan and reducing our environmental footprint?
What we did
Build our new concrete products to last
We created a new product called Lodestar Structures, which are precast concrete modular building units. Our patent-pending Lodestar technology involves a precast concrete floor and a top with four concrete pillars that is modular and that can be stacked one on top of another. We wanted to develop a product that could withstand wind, snow and earthquakes.
We incorporated all that into the design of our Lodestar structures. Having been in the Ontario infrastructure market and making a lot of bridges and box culverts with a design life of 100 years, we decided to put the same quality or better concretes into houses.
Cut waste in innovative ways
We looked at our processes. One of the biggest waste stream is the number of contractor trips to a job site. On our renovation projects, it was astonishing how much the contractors were not at the house working, and they were actually driving to go get parts. Almost every single day, every single contractor had to make a trip back to the store to pick up more parts. If it takes six months to build the house and you’ve got six or eight contractors, in the end, you realize that they spend a lot of time and fuel driving back and forth instead of building your house.
Since our Lodestar structures are precast and stackable, the waste created is minimum because it cuts down on the number of trips that are required, and material and labour waste has been designed out.
We also changed the design of the structures by reducing the number of legs of our Lodestar structures from six to four and thinned the roof and floor slab by 20%.
Reduced toxic materials in our precast concrete
Steel reinforcing adds significantly to the global footprint potential of concrete and it also is the number one factor for the degradation of the concrete long term. When it rusts, it expands, and when it expands, it starts to blow the concrete apart. This why we have engineered out as much of the metal reinforcing as possible. For example, our precast wall panels use glass fiber reinforcing rather than steel reinforcing. We also don't use glues in our Lodestar structures. Glues have very many toxic things that release gas into our houses.
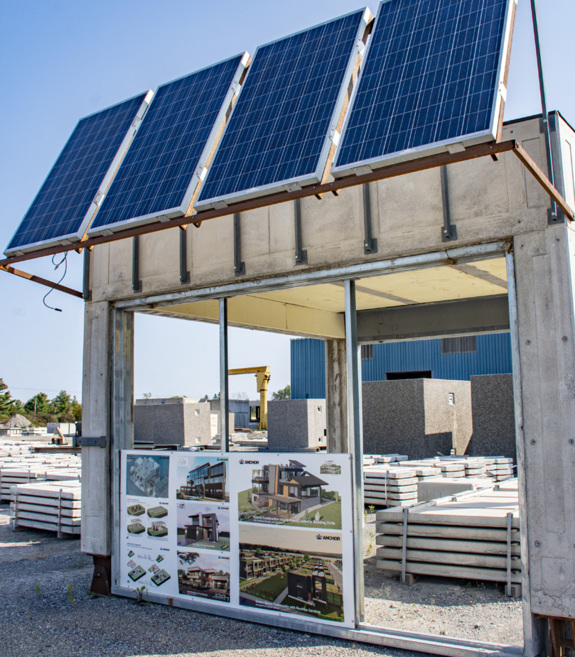
How it turned out
20 days off construction time
…by building with Lodestar Structures compared to building a wood framed detached house. With no on-site assembly, the staff required is reduced, there is no material waste and it also requires fewer deliveries.
20% less concrete used in newer designs
This translates into cost savings for our clients and a lower carbon footprint of our products.
Challenge
We were overpaying for our electricity bill
In 2015, we were looking at ways to cut costs. Lighting was an obvious first step. Our electricity bill was getting higher every month and we also saw that our peak demand charges (the fees from the utility provider based on the intensity of power required at a specific period) were just simply wasteful.
What we did
Switched to LED lighting and reduced our peak demand charges
Adequate lighting is essential in a precast plant and also one of the most important costs. We switched to new, high-efficiency LED lights to significantly reduce our utility bill and also provide employees with a brighter working environment.
Before making the switch, we put up test lights and asked our employees for feedback. One employee suggestion was to include automatic, area-specific sensors that turn lights on and off according to where workers are on the plant floor. This feature is especially useful in swing shifts when some areas of the plant are inactive.
Reduced total demand on our motors at the primary manufacturing time
Making concrete is a lot like a like a cake recipe. You must have all the ingredients exactly right and the right temperature. We’ve been trying to use the advantages of heat, natural heating and cooling as much as possible to reduce our energy consumption. For example, during the summer, we bring aggregates (the granular materials such as sand, gravel and crushed stone that go into concrete) indoors in the early morning so that they don't get heated by the sun. This reduces the energy it takes to manually cool or heat our materials to the right temperatures before mixing.
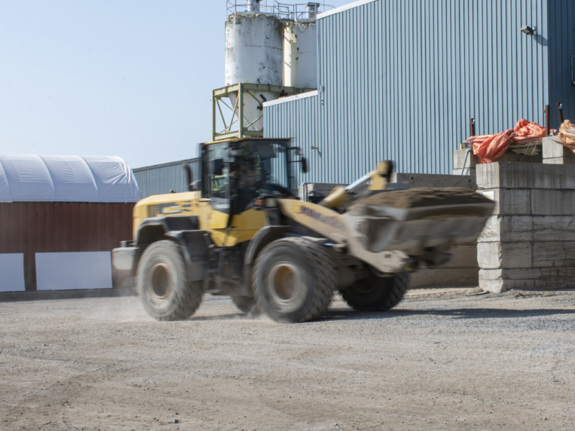
How it turned out
Cut our electrical consumption by about 10%
By switching out to LED lighting, we managed to cut our electrical consumption by about 10%.
Cut out peak demand charges by 30-40%
In total we’ve been able to cut our electricity costs by 20% by also cutting our peak demand charges by 30 or 40%.
Want to learn more about saving energy? Discover how to maximize your equipment efficiency
Challenge
Trucking in water was too expensive
Anchor is not on municipal water. For many years we survived by using well water and using trucked water when our well couldn't keep up. About 10 years ago our well got old and tired, so we started paying a lot to have all our water trucked in.
What we did
Drastically reduced our water usage
Being both cost and environmentally conscious we decided to cut our non-process water usage. That is, water not used in manufacturing. It is difficult to reduce the minimum amount of water used in any given concrete mix.
We changed all our taps to infrared on/off. We changed our toilets to low-volume water usage, and we added a number of waterless urinals in our two manufacturing plants. Finally, we put water meters at the source for all our three locations.
Began harvesting rainwater for our use
We have a large storm water detention pond and we are sequestering the water off of our site. We hope by the end of this year to use 100% harvested rainwater for both process and non-process use.
How it turned out
Reduce water usage per person/per day by about 50%
When it comes to making a positive environmental difference, reducing our water waste makes a big difference in having water when you need it, reducing water costs and reducing sewage treatment/pumping costs. Our average water use per person at Anchor is 4 to 5 times lower than the average Ontarian.
Our roadmap
1969
My parents, Howard and Barbara Bradfield, started Anchor in a hangar at Kingston Airport. Within one or two years, they were selling enough septic tanks to allow them to buy a 10-acre property on Sydenham Road, in Kingston, and started specializing in precast concrete fabrication.
1983
Coming out of university I decided to join the family concrete company.
2001
I bought the business. Anchor evolved and diversified its operations into various lines of business.
2015 – 2019
Big change! We sold off three different product lines that used to make up about 75 to 80% of our annual sales, leaving us only with about a fifth of our previous sales revenues. We let go of everything that didn’t fit our vision of wanting to build financially and ecologically sustainable homes, products and communities.
2021
The business split into three companies: Anchor Concrete (precast concrete fabrication), Anchor Rebar Supply (custom rebar solutions) and Lodestar Structures (precast concrete modular, building units).
2023
With over 50 countries interested in licensing our Lodestar system, we continue to be focused on innovation and efficiency to deliver the best products and lower our carbon footprint, and that of communities around the world.
Jeff’s final thoughts
A lot of people think I'm crazy because we sold three different product lines that used to make up about 75 to 80% of our annual sales. We sold off pretty much everything that we thought didn't fit the mold: build an innovative, sustainable business that can lead us to a better world.
One of my favourite books and a guiding light for me as an entrepreneur is Cradle to Cradle: Remaking the Way We Make Things. It was written by an architect and a chemist, and the essential idea is that waste is a 100% human concept. Nature does not have the concept of waste. Everything can be a resource for something else. We try to apply these principles at Anchor and Loadstar: when we see an opportunity to save a dollar or kilogram of CO2, we’ll do it.
Many business owners think that being green is a costly process, but I like to think about it the other way around: being smart and being more efficient can help your business, and often it will be good for the environment too.